El gerente de proyectos de una planta de detergentes en México, tenía como objetivo modernizar su proceso y eliminar los paros de planta. Ya que el mismo comenzaba a verse afectado por paros de planta inesperados, por carencias que tenía el sistema que se implementó en unas décadas atrás el cual contaban con un sistema con dos aplicaciones idénticas de monitoreo en intouch de la marca Wonderware alojadas en servidores físicos independientes ya con poca capacidad con sistemas operativos viejos y un controlador central obsoleto de la marca Rockwell.
El Problema
Necesitaba acondicionar y actualizar el sistema a las nuevas tecnologías que le permitan tomar decisiones para evitar problemas con los equipos de planta y así como mejorar la efectividad y rentabilidad de la producción.
Para disponer de la información del proceso, el gerente de producción asigna operadores para recorridos periódicos en los 3 turnos para recorrer las máquinas y la instrumentación llevando un registro manual en una bitácora, esta tarea representaba un gran esfuerzo adicional, la información llegaba tarde y la información no era confiable dado que había errores al momento de capturar la información en la bitácora manual o al trasladar la información a tablas de Excel para su análisis.

Los equipos de control que actualmente tenían estaban obsoletos, lo que dificultaba encontrar refacciones nuevas y en caso de encontrarlas el costo era excesivo ó se tendría que buscar el equipo usado sin garantía, pero se tenía que considerar esta variante dado que en alguna falla mayor obligaría al sistema a parar la planta y tener pérdidas económicas muy grandes y comprometer la producción a los clientes.
Capacidades
El gerente de proyectos nos comentó que estaba buscando un sistemas de automatización de procesos para la fabricación de detergentes de última generación que le permitiera monitorear en tiempo real en todo momento considerando todos los puntos anteriores, para poder tomar acciones en tiempo y evitar tener consecuencias mayores como lo es un paro prolongado de planta y evitar gastos innecesarios.
El Resultado
Pudimos cumplir con todos estos requerimientos mediante un sistema automatización de procesos para la fabricación de detergentes innovador integral de monitoreo en tiempo real de última generación, permitiendo conocer los datos para su análisis y toma de decisiones inteligentes sobre la producción y mantenimiento de sus equipos, comentan que el seguimiento es ahora mucho más sencillo al recibir mensajes de alerta para situaciones criticas y el poder monitorear el sistema desde fuera de planta en cualquier momento.
Se actualizo el sistema de control y se documento la programación lo cual hace más amigable la intervención para mantenimiento y/o ajustes en la programación.
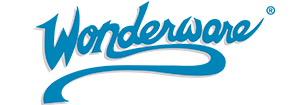